臺達 3C 電子智能制造方案,全面提升工廠生產力
文:臺達2021年第二期
面對全球智能制造浪潮,制造工廠轉型刻不容緩。臺達自動化點膠解決方案可隨產線追蹤工件或產品,自動補償并調整機器人移動距離,精確控制點膠位置與出膠量,打造一體化的工作站。臺達DIAMES制造執行管理系統 以 IPO(Inputs/Process/Outputs)的方式,全面整合工廠資源,提升工廠效能、質量、生產力,達到精益生產與持續改善的目的。
文/臺達-中達電通
臺達自動化點膠解決方案,實現精準膠量控制及多角度作業
隨著工業技術迅速發展與推進,各種電子產品的元件在制程都需要進行點膠。由于人工作業無法精確、穩定的控制出膠量,容易導致質量不一、甚至不良品情況。點膠機的誕生取代大量人工作業,是許多產業不可或缺的設備,如3C與汽車等的電路板、IC封裝、光學器件加工、電子電路元件與印刷電路板粘接、照明設備、各種機殼粘接,手機屏幕、邊框和各種面板防水封裝等。
點膠工藝與技術隨著各種產品的小型化及復雜化而日益發展,并結合工業機器人達到多面向點膠。三軸、四軸的點膠機雖已普及多年,卻因機器人動作軸向與旋轉角度限制而無法達到高速運行,并可能精度不足和無法穩定點膠。因此,臺達提出自動化點膠解決方案,能精準控制膠量及點膠位置,并采用五軸機器人(SCARA機器人加上第五軸),點膠頭能正負360°旋轉,改善三軸與四軸的動作缺陷,達到多角度快速點膠。
臺達將自動化點膠解決方案應用于自身的吳江生產研發基地可編程控制器生產線,利用五軸機器人依照 PCB板的Gerber檔點位設定運動路徑,并跟隨生產輸送帶上的 PCB 板;搭配機器視覺系統打造一體化智能工作站,自動調整機器人距離,以高自由度軸快速到達指定位置并控制出膠量,精確完成點膠。
臺達自動化點膠解決方案采用自行開發的PC-Based工業運動控制器 MH1 及五軸機器人,可精確控制點膠,客戶也可通過簡易操作界面快速建立項目及設置運動路徑。作業時搭配機器視覺系統 DMV2000 拍照取得工件坐標,可自動補間調整工件或產品在輸送帶上的移動距離。點膠過程無需使用任何定位治具,PCB 板可隨意角度擺放,并且經由人機界面呈現供膠及機器人動作相關參數,可實時監控工況、減少瑕疵,生產效率也大幅提升。若搭配工廠制造管理系統(MES)可將制程參數上傳數據庫進行數據追蹤與生產管理。臺達自動化點膠解決方案提供效益如下:
? 一體化設備自動化生產,無縫整合:無縫整合臺達自行研發、制造的工業機器人、機器視覺、運動控制器與人機界面等關鍵元器件,實現自動化快速、平穩生產,為客戶打造一體化工作站,取代人力、提高產量及效率,使用及維護也更便捷;
? 五軸機器人高自由度動作,縮短移動時間:五軸機器人控制點膠頭正負360°軸向旋轉、水平正負70°翻轉,多角度作業并避開障礙,使工作軌跡更快速,縮短點膠時間;
? 自動補償點膠位置:通過機器視覺系統 DMV2000 取得工件坐標并輸出自定義的旋轉中心后,機器人可自動補償工件在輸送帶上移動的距離,讓點膠位置更精確;
? 簡易操作界面、快速建立多個項目,隨時彈性換線:整合視覺及機器人相關參數設定,可經由 DXF 檔解析或 PCB Gerber 檔點位快速建立多個項目,實現靈活換線,滿足客戶彈性生產需求;
? 實時監控參數及輸出信息:通過臺達人機界面顯示定位距離、位置、速度及膠桶重量等參數數據,并提供實時監控,客戶可快速依狀態調整參數,靈活作業;
? 異常警報,確保人員安全:設備在作動過程中若出現異常,會自動發出異常警報,并即刻停機,確保人員安全無虞,客戶也能實時排除故障。
臺達智能制造解決方案, 助力電子組裝企業推行信息化進程
隨著全球制造業邁入智能制造,企業以智能優化生產制造,提升企業市場競爭力,已是必然趨勢。傳統電子組裝行業,貼片機上料防錯、錫膏及濕敏元件在線使用管控、鋼網使用次數統計等都是通過傳統的人工作業方式,容易出錯并造成品質不良,并且影響生產。此外,生產進度及庫存狀態無法實時掌握、設備/物料異常無法及時處理、設備參數需手動調整、信息不透明、貼片機無低位預警、焊點位置度測試/功能測試無SPC管制等問題也一直困擾電子組裝業企業。
在面對少量多樣的訂單時代,市場的需求日益復雜,越來越多的電子組裝企業發現,工廠目前的信息化水平很難滿足多樣化、客制化的需求,對企業精益化管理也帶來極大挑戰。因此,發展MES技術成為電子組裝業推行信息化進程中舉足輕重的一環。
臺達DIAMES制造執行管理系統 以 IPO(Inputs/Process/Outputs)的方式,從前期準備(工廠建模、料卷/料槍/鋼網/刮刀等條碼化、物料 BOM 展開等)到執行過程監控(上料防錯、治具使用壽命管理、即時數據收集、看板管理、自動化整合等),再到數據、報表的效益分析,進而管理,達到精益生產與持續改善。臺達最新解決方案從診斷到元件管理都不用人員監管。
臺達為某領先精密光電薄膜元器件制造商提供了一套完整的電子組裝業數字化工廠解決方案,主要通過臺達 DIABCS整線自動化控制系統搜集所有設備資料與數據,上傳 DIAMES 制造執行管理系統,實現制品管理、設備管理、質量管理、異常分析、預防保養等功能。方案并與 ERP、WMS 等系統整合,幫助企業整合計劃、生產、倉儲等環節,達到內部信息協同化與透明化。
針對表面粘著 (SMT) 制程普遍關注的重點, DIAMES的SMT模組提供相對應的解方,包含:
上料防錯:通過掃描物料、料槍及料架站位條碼,與系統中料站表作比對,一致則通過,不一致則警示;支持替代料的管控。
低位預警管理:實時獲取貼片機耗料、拋料信息;當剩余數量低于設定的預警管控線時,觸發低位預警,并通知倉庫提前備料,實現 JIT (Just In Time)供料。
濕敏元件管理:設定濕敏元件等級代碼及允許暴露時間;管控濕敏元件時效性,避免元件質量異常造成成本浪費。
治具管理:機種使用鋼網/刮刀防錯管理,提供追溯查詢分析;鋼網/刮刀使用次數記錄,達到使用預警次數提示保養,超過上限次數,報警管控;領用、歸還時提供治具量測功能,確保質量。
錫膏的全生命周期管理:計算回溫時間,回溫時間未到和超過進行報警或報廢;開封以后開始使用,開封未用完的進行回存,并進行機種“防呆”校驗。
臺達DIAMES 成功扮演了智能制造承上啟下的角色,將計劃層與現場設備層無縫對接起來,執行 ERP 系統制定的生產計劃,整合工廠內、外部資源,提升生產效率和管理執行能力,從設備層、控制層、管理層三層搭建智能工廠。在實際上線使用后,臺達 DIAMES制造執行管理系統的智能制造應用為客戶帶來以下效益:
l 提升生產力:低位預警,提前備料,減少待機時間;節省近半的備料周期工單完工清尾時間;
l 提升質量:實時的質量異常管制,掌握不良率狀況,讓人員持續追蹤和管制不良品的處理;通過日本原廠稽核;達到0錯料事故月發生率;
l 提升效能瓶頸:上系統后每顆鏡頭的檢查時間縮短約50%,節省約75%的換線時間。
面對全球智能制造浪潮,制造工廠轉型刻不容緩。通過信息整合與數據分析回饋,工廠能提升營運水平,達到降低成本、提高產值,同時積極與具備產業知識、實戰經驗的伙伴合作,根據自身工廠需求逐步轉型智能制造,才是致勝的關鍵。
中傳動網版權與免責聲明:
凡本網注明[來源:中國傳動網]的所有文字、圖片、音視和視頻文件,版權均為中國傳動網(www.hysjfh.com)獨家所有。如需轉載請與0755-82949061聯系。任何媒體、網站或個人轉載使用時須注明來源“中國傳動網”,違反者本網將追究其法律責任。
本網轉載并注明其他來源的稿件,均來自互聯網或業內投稿人士,版權屬于原版權人。轉載請保留稿件來源及作者,禁止擅自篡改,違者自負版權法律責任。
如涉及作品內容、版權等問題,請在作品發表之日起一周內與本網聯系,否則視為放棄相關權利。
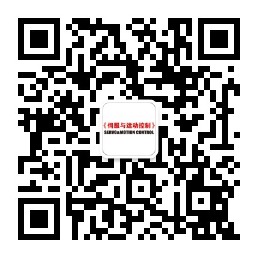
關注伺服與運動控制公眾號獲取更多資訊
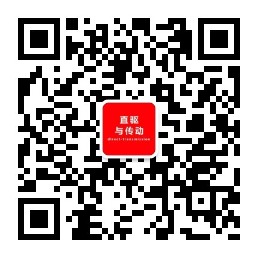
關注直驅與傳動公眾號獲取更多資訊

關注中國傳動網公眾號獲取更多資訊
- 運動控制
- 伺服系統
- 機器視覺
- 機械傳動
- 編碼器
- 直驅系統
- 工業電源
- 電力電子
- 工業互聯
- 高壓變頻器
- 中低壓變頻器
- 傳感器
- 人機界面
- PLC
- 電氣聯接
- 工業機器人
- 低壓電器
- 機柜